Harnessing AI for Predictive Maintenance in Modern Manufacturing
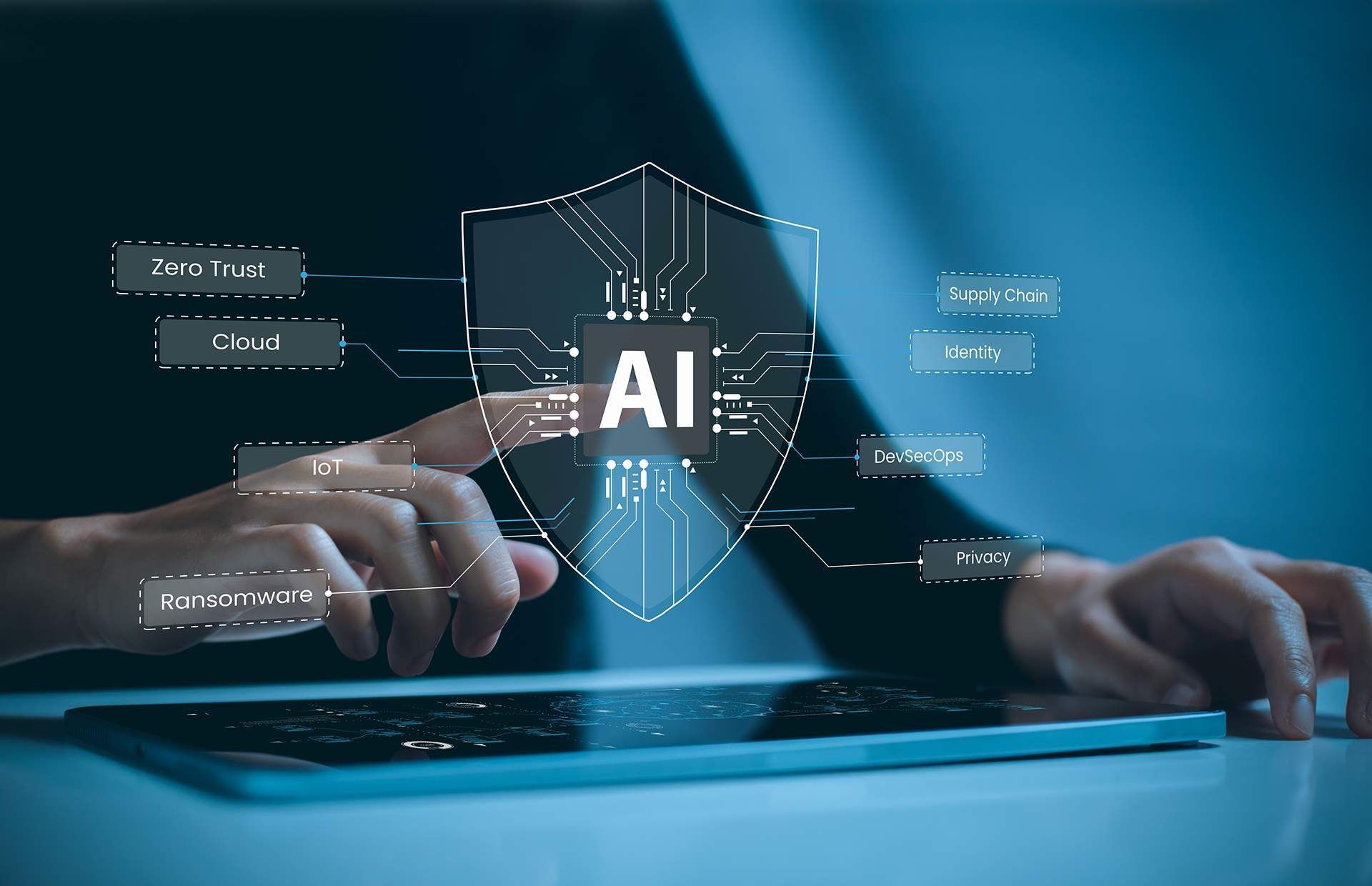
Introduction
In the modern manufacturing landscape, efficiency, reliability, and proactive planning are paramount. Predictive maintenance, empowered by artificial intelligence (AI), is revolutionizing the way manufacturers manage assets and minimize downtime. This blog explores how AI-driven predictive maintenance is changing the industry, from machine learning algorithms to real-time condition monitoring, and how strategic advisors like ATG Advisors, along with our technology partners, including Perimity LLC, help businesses effectively implement these solutions.
The Evolution of Maintenance: Reactive → Preventive → Predictive
Traditional maintenance methods relied on reactive responses—fixing machines after breakdowns. This approach led to unplanned downtime, loss of production, and high repair costs. Preventive maintenance improved upon this by scheduling service at regular intervals, often based on manufacturer recommendations. However, it frequently resulted in unnecessary part replacements and labor, ultimately inflating operational costs.
Predictive maintenance (Pd.M), by contrast, uses real-time data to predict failures before they occur. Sensors and AI algorithms monitor equipment conditions continuously, enabling maintenance only when it's truly needed. This model reduces waste, enhances uptime, and increases asset longevity.
ATG Advisors’ Role: ATG Advisors helps manufacturing clients transition from preventive to predictive models by assessing operational readiness, identifying suitable assets, and coordinating technology implementation through our partners like Perimity LLC and other vetted solution providers.
What is Predictive Maintenance?
Predictive maintenance involves using data analytics, machine learning, and sensor technology to assess the current condition of equipment. Rather than relying on a fixed schedule, systems track variables such as temperature, vibration, and pressure to forecast issues with high precision.
Key components include:
- IoT sensors: Gather real-time operational data on machinery performance.
- AI/ML models: Analyze historical and live data to detect anomalies.
- Cloud computing: Stores and processes vast datasets to derive actionable insights.
- Maintenance software: Provides intuitive dashboards and alert systems for field technicians.
ATG Advisors’ Role: We provide strategic oversight and project management, ensuring seamless integration of IoT sensors, ML modeling, and cloud infrastructure via trusted partners like Perimity LLC, who specialize in secure system deployments.
Key Technologies Enabling Predictive Maintenance
- Machine Learning (ML): Trains algorithms on large data sets to detect subtle deviations from normal operations, enabling early intervention.
- Digital Twins: Virtual replicas of physical assets that mirror operations in real time, helping predict wear and simulate potential failure scenarios.
- Edge Computing: Processes data closer to the source (e.g., on-site) to reduce latency and improve decision-making speed.
- 5G Connectivity: Enables high-speed, low-latency communication for continuous data transfer and remote monitoring.
- Big Data Analytics: Integrates data from multiple sources (e.g., ERP systems, machine logs, environmental sensors) to paint a comprehensive picture.
ATG Advisors’ Role: Through our alliance with Perimity and other enterprise-level vendors, ATG Advisors guides clients through technology selection, integration design, and performance benchmarking to ensure the solution meets both technical and strategic goals.
Case Study: Predictive Maintenance in the Automotive Industry
A leading automotive manufacturer integrated PdM across its robotic assembly lines. By equipping robots and conveyors with vibration and thermal sensors, the company reduced unexpected breakdowns by 42% and maintenance costs by 30%.
AI models detected early signs of wear in robotic arms, allowing teams to replace parts before failure. Additionally, downtime across lines dropped significantly, boosting overall throughput and meeting production targets more consistently.
ATG Advisors’ Role: For clients in similar sectors, ATG Advisors deploys strategy-led engagement models. Our technology partners handle implementation and data modeling, ensuring solutions are aligned with client production goals and manufacturing timelines.
Benefits and ROI of Implementing AI-Based Systems
- Reduced downtime: Avoid unplanned outages that stall production lines.
- Cost savings: Minimize overtime labor and reduce inventory of spare parts.
- Extended equipment life: Maintain machinery under optimal operating conditions.
- Improved safety: Prevent hazardous failures and workplace incidents.
- Data-driven decisions: Optimize scheduling, budgeting, and capital planning.
A McKinsey study found that predictive maintenance can lower maintenance costs by 10-40% and reduce downtime by up to 50%, with average ROI realized within 12 to 24 months of full-scale deployment.
ATG Advisors’ Role: We assist with strategic modeling of ROI scenarios and lead executive briefings to justify capital expenditure. Implementation is carried out in collaboration with Perimity LLC and our partner network.
Implementation Steps
- Asset Inventory: Identify critical machines based on historical downtime and production dependency.
- Install Sensors: Select and install IoT sensors for parameters such as vibration, humidity, thermal readings, etc.
- Data Infrastructure: Configure edge gateways and cloud environments for secure, scalable data management.
- Model Training: Use historical and real-time data to train and fine-tune machine learning models.
- System Integration: Connect PdM systems with ERP/CMMS for seamless task assignment and reporting.
- Pilot Program: Implement on a small scale to assess model accuracy and fine-tune deployment.
ATG Advisors’ Role: ATG coordinates and oversees the entire implementation process, while our technology partners deliver the technical configurations. This dual-layered approach ensures strategic alignment and technical precision.
Common Challenges and Solutions
Data Quality: Poor sensor data leads to false positives/negatives and undermines trust in the system.
Solution: Through our partners, we source high-quality, industry-certified sensors and conduct data validation protocols.
Resistance to Change: Technicians may distrust or override AI-generated alerts.
Solution: ATG Advisors facilitates stakeholder onboarding and change management through tailored workshops and hands-on demonstrations.
Cost of Implementation: Upfront investment may appear high without clear ROI projections.
Solution: We prioritize phased rollouts and provide detailed ROI forecasts to justify spend and secure funding.
Future Outlook
The next phase of predictive maintenance includes:
- Autonomous systems that order parts and schedule service windows without human input.
- Greater integration with digital twins for simulation-based planning.
- Self-learning AI systems that continuously improve prediction accuracy.
- Use of augmented reality (AR) for real-time remote assistance during equipment servicing.
ATG Advisors’ Role: We continuously evaluate new innovations across our partner ecosystem—including Perimity LLC—and recommend emerging solutions that keep our clients on the leading edge of operational technology.
Conclusion
Harnessing AI for predictive maintenance is transforming the manufacturing sector. From reducing downtime to extending machine life, the benefits are clear. With ATG Advisors as a strategic partner—and through our collaborative work with Perimity LLC and other leading technology providers—manufacturers can navigate the complexities of PdM deployment with confidence.
Investing in this technology today sets the foundation for a smarter, more resilient tomorrow.
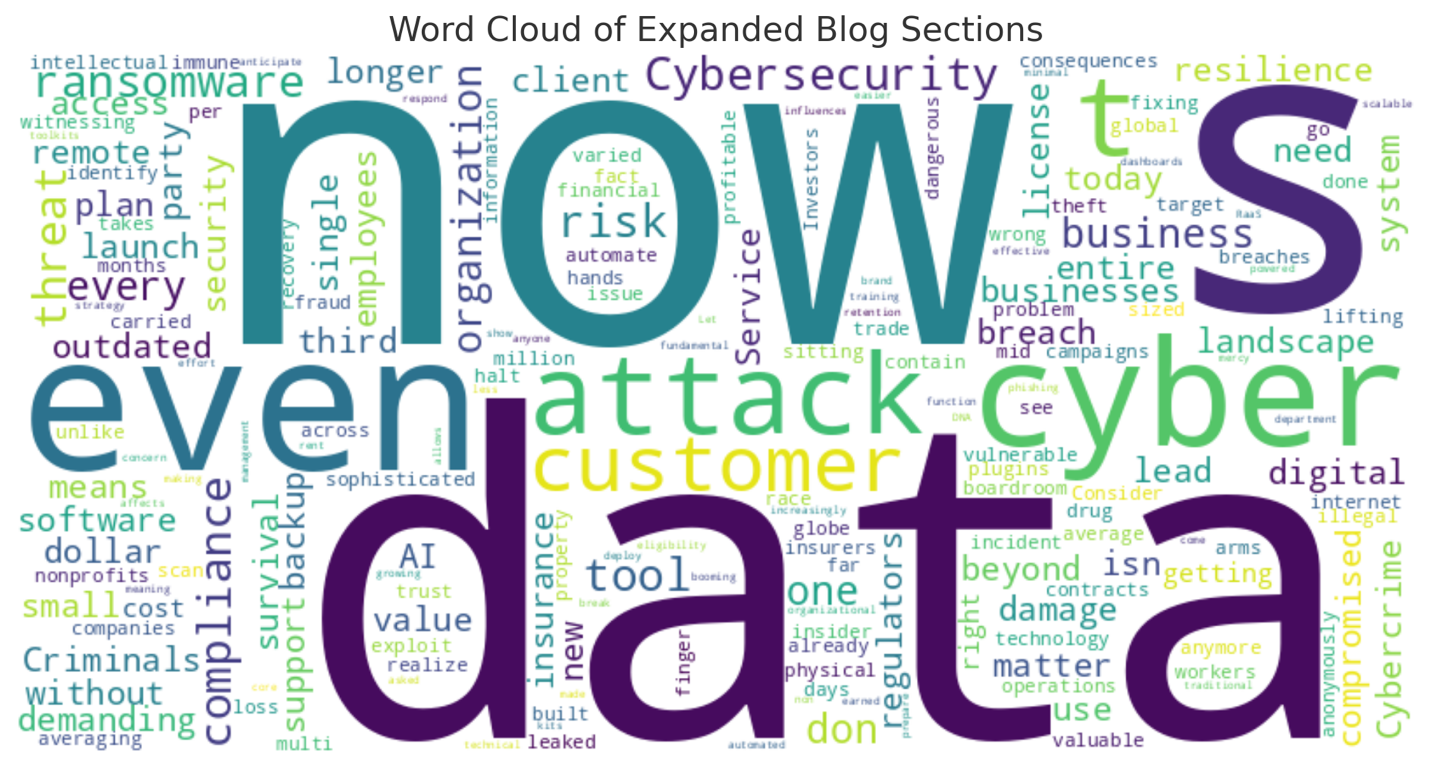
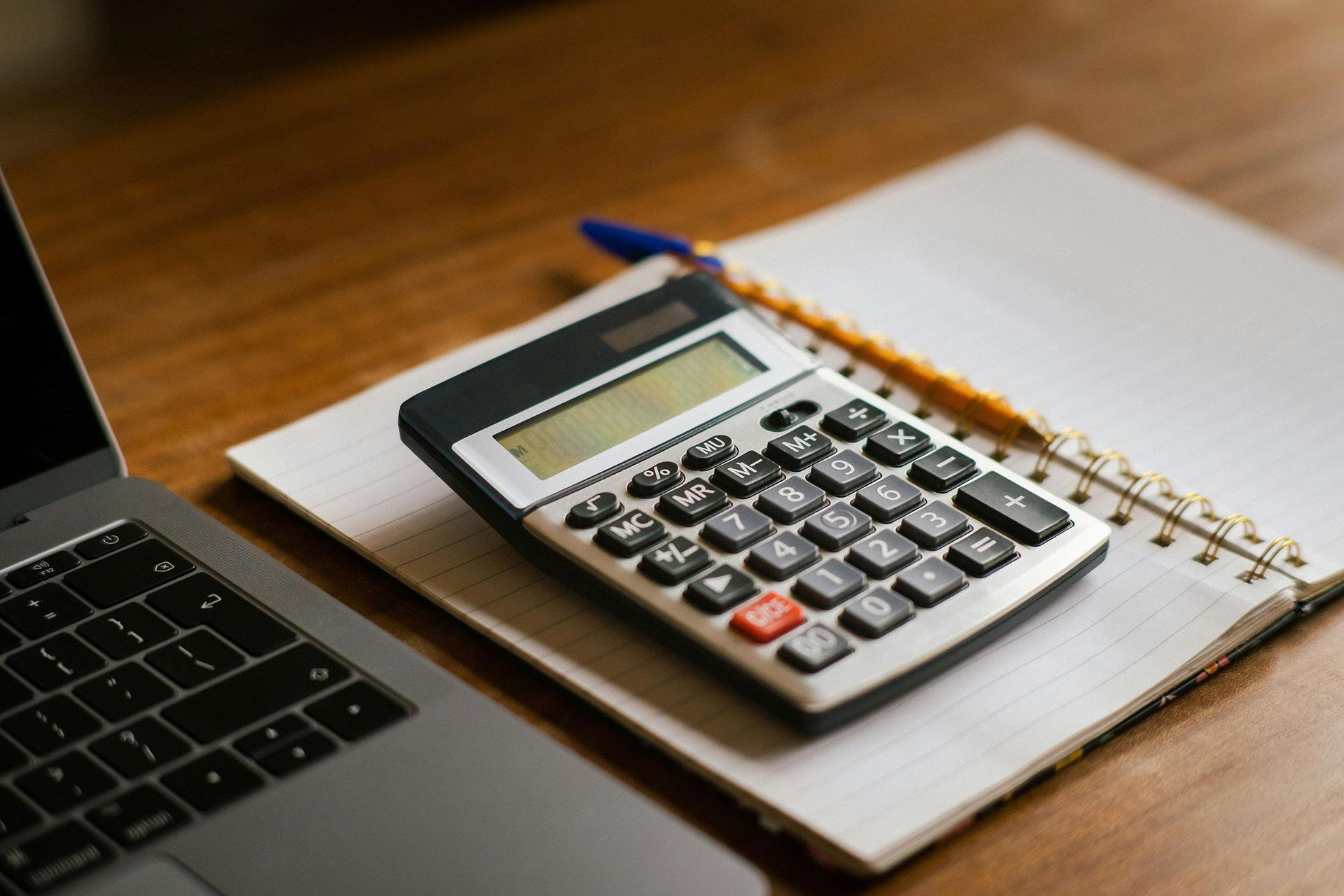
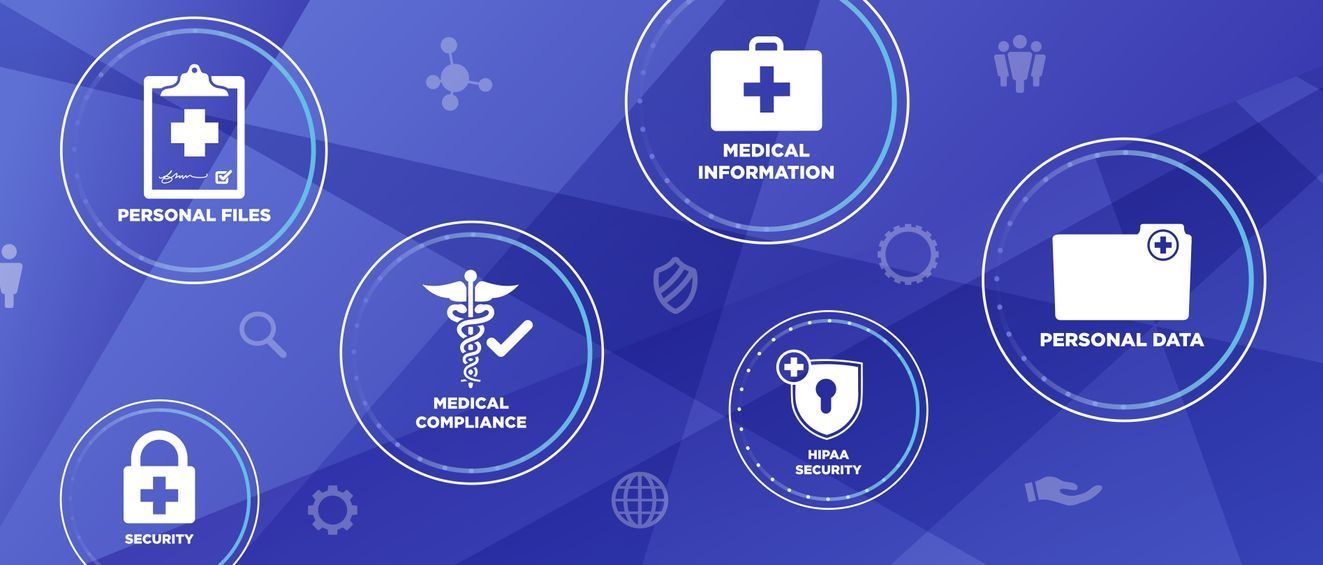